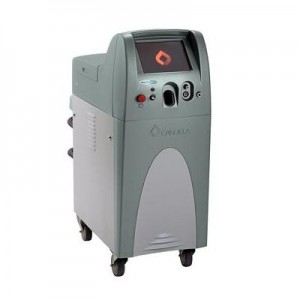
Custom Thermoforming Process:
- Design: CAD model or drawing
Each thermoformed part starts with a concept and a design. We can work from your drawings and CAD files or our in-house engineering team can partner with you to bring your concept to a finished design with drawings & CAD files ready for production. We can also work with you to refine your design for manufacturability. - Material: ABS, HDPE and Kydex (PVC/Acrylic blend) are most common; wide selection available
We work with a wide variety of thermoplastic materials. Common materials such as ABS, HDPE, Kydex, Acrylic, PETG, and Polycarbonates are readily available. We can also process specialty materials such as Ultem, Polysulphone, and PC/ABS blends among others. We can help you select the best material for your application based upon cosmetic needs (color, texture, gloss & finish) along with functional requirements (rigidity, Flame Retardant, impact strength, chemical resistance). - Tooling: Aluminum mold used in forming
The mold provides the form to create the part shape during the forming process. The mold can be a male or female molding depending upon the part characteristics and design. Most production molds are temperature controlled aluminum molds which may be cast or machined. We can also create soft tooling for prototyping or very low volumes. Universal Plastics offers in-house tooling capabilities which reduces both cost and production time. - Forming: Heating the mold to shape the part
After the part is formed, it needs to be trimmed to remove the flashing and create the cutouts and contours required on the finished part. At Universal Plastics a majority of our trimming is done on 5 Axis CNC routers which allows to offer precise control, tolerancing, and repeatability. Each facility has numerous 5 axis CNC routers. - Routing: Trimming the formed part
The formed part is trimmed to remove excess material and cut shapes within the part. Universal Plastics has 53 routing machines, including 26 fully robotic 5-axis routers which trim complex shapes precisely and at high speed. - Secondary Operations: Complex assemblies, painting, silk-screening, EMI-RFI shielding
Complex Assemblies, Painting, RF/EMI Shielding, and silkscreening. Many parts require additional fabrication beyond the forming and basic trimming operations. Universal Plastics has always taken pride in our ability to offer a full complement of secondary services. This includes complex assemblies. Bonded mounting blocks, ribs, and threaded inserts are all routine for us. We can also provide and install hardware such as hinges, latches, ball studs, rivets, custom metal bracketry and others. Our finishing department can perform finish painting in both a textured or smooth finish. We can also apply a conductive coating to provide RF/EMI protection. Pad printing and silkscreening services are also available.
Advantages:
Custom thermoforming is a plastic manufacturing process which allows you to create larger plastic parts with a much lower tooling cost than other plastic processes. With thermoforming, you can add style and functionality that just can’t be achieved with sheet metal, without the high tooling costs of other molding processes. Furthermore, thermoformed products can be formed from the same plastics, so there is no need to compromise on physical properties. Thermoformed sheet can be made with high impact and flame retardant properties, and in an infinite range of colors. It is the ideal process for large complex shaped parts at low volumes. Custom thermoforming is often an excellent alternative to injection molding which has a higher initial tooling costs and minimum quantities. Universal Plastics also offers injection molding, so we can work with you to understand the best manufacturing process for you based on your part volume, design and other needs. We pride ourselves on our ability to offer unbiased, process-agnostic advice and multiple production processes for high mix / low volumes, low mix / high volumes and the breadth in between.
Applications:
Custom thermoforming is widely used in virtually every industry. Common applications include machine housings, bezels, and enclosures, which gain style and user appeal with thermoformed plastics. Custom material handling trays can be designed specifically to your requirements with a much lower tooling investment. Outdoor enclosures and equipment covers can exhibit a contemporary style that defines your brand and sets you apart from traditional boxy sheet metal covers. Custom thermoformed part protection covers and trays are used to safeguard and transport expensive machinery. With weatherable properties added in, you can feel confident in the durability of thermoformed products, which won’t fade, rust, or crack under stress. Even scientific equipment can be made more stylish and distinctive with thermoformed plastics, giving you a critical edge over your competitors.
Custom Thermoforming Capabilities at Universal Plastics:
Universal Plastics is the largest precision heavy gauge custom thermoformer in the Northeastern US with an asset base of 22 pressure formers, 14 vacuum formers and 26 5-axis trimming machines, supplying our customers with vacuum forming, pressure forming, including twin sheet forming and complex assemblies, with part sizes up to 12’ x 9’. In addition, we offer in-house tooling, an experienced engineering staff, and a full complement of secondary/finishing services, including our new state of the art paint booths which can produce automotive quality finishes. With a range of rotary formers, rapid manufacturing processes, and a global supply chain, we can produce thermoformed parts at the most competitive prices.
In addition to custom thermoforming, Universal Plastics also offers injection molding (including gas assist and structural foam molding) and custom blow molding. We would be glad to talk with you about the optimal process for your needs.
To discuss how Universal Plastics can meet your needs, please contact us.