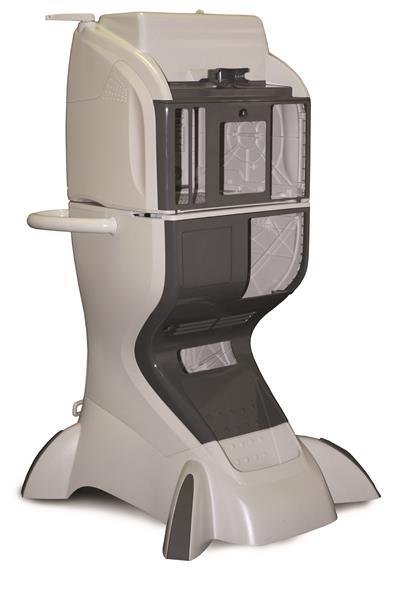
Large Part, Low to High Volume Injection Molding Capabilities:
Universal Plastics has expertise in medium to larger sized complexly designed plastics parts, but we have the capability to produce almost any size part. Universal Plastics is more than your single source for injection molding. For many years, we have been providing high quality parts. Our injection molded parts include plastic covers, plastic trays, plastics shrouds, plastic panels and plastic housing for the medical, business, financial and laboratory markets. Universal Plastics offers many injection molding services to meet your criteria to mold large plastic parts. No matter your requirements, we can offer the proper injection molding process and equipment to distinguish your products from the competition. With services extending from engineering and design to final assembly, cosmetic finishing and shipping, Universal Plastics is a single source for your entire project and complex assemblies. Our portfolio of in-house services can help streamline your supply chain, reduce costs, and shorten lead times. Contact us today to discuss your injection molding needs.
Secondary & Finishing Services:
With services extending from engineering and design to final assembly, cosmetic finishing and shipping, Universal Plastics is a single source for your entire project and complex assemblies. Our portfolio of in-house services can help streamline your supply chain, reduce costs, and shorten lead times and includes: painting, woodshop, tooling, sonic welding, pad printing, complex assemblies, packaging and shipping, etc.
Injection Molding Process & Applications:
Universal Plastics has seventeen injection molding machines with press tonnages ranging from 85 to 1,500 tons. We specialize in large multi-part projects and are valued by OEM customers for our large project design and integration services. We process a full range of engineered polymers and specializes in short run production quantities. We offer the following processes:
- Injection Molding: accomplished by forming molten plastic under pressure into a cavity formed between two matched metal mold halves. Once the plastic cools, the mold is opened and the parts are removed. Used for a wide variety of end-use applications such as medical device panels, diagnostic equipment covers, industrial and commercial equipment. etc.
- Structural Foam: structural foam molding is a low pressure injection molding process that is capable of producing very large, sturdy parts and structural components.
- Gas Assist Injection Molding: by injecting a controlled stream of gas (nitrogen or carbon dioxide) into the mold, thick walls are created with hollow sections that save on material, shorten cycle time, and reduce the pressure required to mold the large plastic parts with complex designs and attractive surface finishes. The process is especially ideal for large handles, equipment covers, doors, bezels, cabinets and skins.
Universal Plastics Overview:
Universal Plastics is a custom plastic products manufacturer with expertise in a range of processes, including custom blow molding, thermoforming, and injection molding (gas assist and structural foam) for the medical, aerospace, transportation and general industrial markets. We have expertise in large, complex and highly aesthetic parts pride ourselves on our ability to offer unbiased, process-agnostic advice and multiple production processes for high mix / low volumes, low mix / high volumes and the breadth in between. All the manufacturing sites within the Universal Plastics family share a long history of providing their customers with high quality, large, complex molded parts and are known for outstanding customer service and engineering support. Each has dedicated staff, operating facilities and processes.
Universal Plastics can meet your end-to-end plastics manufacturing needs – we offer in-house tooling, design & engineering services and a full complement of secondary/finishing services including complex assemblies, high gloss painting (Class A automotive finish), RFI/EMI shielding, drape forming, warehousing, etc. Universal Plastics is ISO9001: 2015 registered. Universal Plastics prides itself on working collaboratively with our customers to improve our business processes, skills and technology to continue to deliver innovative custom plastic product solutions that work at globally competitive pricing. We work with a long-standing and diverse set of customers, from fortune 500 companies, to smaller OEMs to start-ups, in a wide range of industries. Our customers have placed their trust in us to deliver the right product at the right price, the first time. For more information and to discuss how Universal Plastics can put our expertise to work for you, please contact us today.