Universal Plastics is a leading expert in manufacturing large thermoformed parts for the medical, aerospace, recreational products, outdoor lawn equipment, construction, agricultural, traffic, and communications markets.
Thermoforming is often the best choice when looking to manufacture large custom designed parts in low to medium volumes. Universal Plastics has the largest thermoforming machines in the Northeastern US, with the ability to form parts as large as 9’ x 12’. Universal Plastics also offers a full complement of secondary operations, including several state-of-the-art in-house paint booths – we offer class A (automotive finish) high gloss painting for parts as large as 11’x11’x3’. To discuss how Universal Plastics can meet your large plastic parts needs, please contact us.
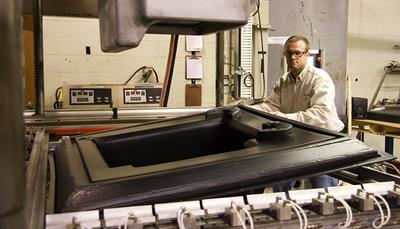
Why is Thermoforming a Good choice for Large Parts?
- Lowest tooling cost to alternatives
- Shorter lead times
- More cost effective and better aesthetics than fiberglass or metal
- Weight reduction – thermoformed parts are about 30% lighter than equivalent fiberglass parts
- Better detail and part reliability
- Ability to combine multiple components into one cohesive part
- Endless choices for color, texture and finish
To discuss how Universal Plastics can meet your large part thermoforming needs, please contact us.
Large Part Thermoforming Advantages:
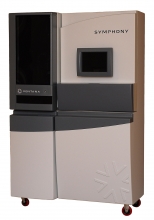
Large Part Thermoforming Applications:
Universal Plastics’ expertise in large thermoformed parts ranging across various industries and product types. Common large parts include:
- Pallets
- Hoppers
- Housings
- Panels
- Enclosures
- Radomes
- Totes
- Bins
- Guards
- Signs
- End caps
Large Part Thermoforming Materials:
A wide variety of material options exist to meet cosmetic needs (color, texture, gloss or finish) or functional requirements (rigidity, flame retardant, impact strength, chemical resistance) and simplify the finishing process. Contact us — Universal Plastics will share our expertise in thermoplastics to help you to find the right material for your part.
Materials used in thermoforming process include ACRYLIC, ABS, Kydex, HDPE, LDPE, PP, PVC, PETG, and polycarbonates. For a full list of our materials see our materials page.
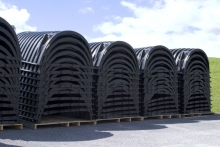
Large Part Thermoforming Capabilities at Universal Plastics:
Universal Plastics is the largest precision heavy gauge custom thermoformer in the Northeastern US with an asset base of 22 pressure formers, 14 vacuum formers and 26 5-axis trimming machines, supplying our customers with vacuum forming, pressure forming, including twin sheet forming and complex assemblies, with part sizes up to 12’ x 9’. In addition, we offer in-house tooling, an experienced engineering staff, and a full complement of secondary/finishing services, including our new state of the art paint booths which can produce automotive quality finishes. With a range of rotary formers, rapid manufacturing processes, and a global supply chain, we can produce thermoformed parts at the most competitive prices.
In addition to custom thermoforming, Universal Plastics also offers injection molding (including gas assist and structural foam molding) and custom blow molding. We would be glad to talk with you about the optimal process for your needs.
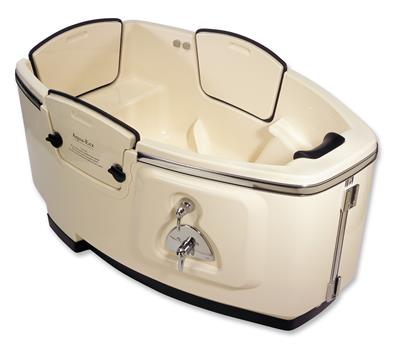