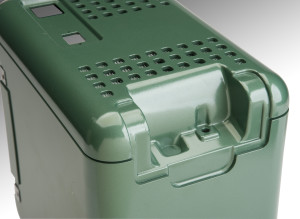
Pressure Forming Process:
Pressure forming is an advanced plastic manufacturing process whereby a plastic sheet is molded to a complex and detailed shape utilizing a single-sided mold to create the formed shape using vacuum & pressure on opposing sides of the sheet. Pressure forming is an enhancement to the vacuum forming process. With traditional vacuum forming, the parts are being formed by creating a vacuum on the mold side of the sheet. Since atmospheric pressure is 14.7 pounds per square inch (PSI) this is the theoretical maximum forming pressure available with vacuum forming. With pressure forming, a pressure box is added to the non-mold side of the sheet. The hot plastic sheet creates the seal between the pressure box and the mold. Air pressure up to 60 PSI is then added to the non-mold side of the sheet in addition to pulling the vacuum on the mold side. This can effectively increase the forming pressure 3 to 4 times what is available with vacuum forming. Universal Plastics’ sales and engineering teams can provide you with guidance on selecting the right plastic manufacturing process for your needs. If pressure forming is right for you, we will convert your design to a 3D model for manufacturing.
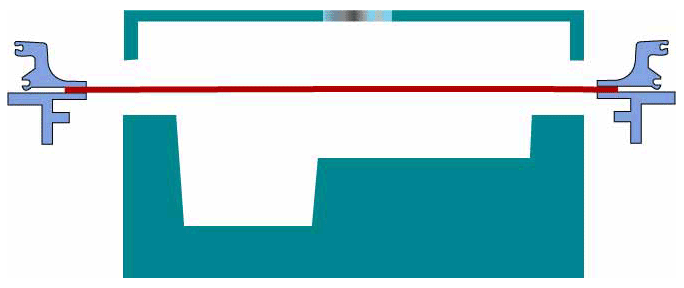
Advantages:
This added forming pressure enables creating thermoformed parts with much sharper detail. The appearance on the mold side of a pressure formed part can look virtually identical to an injection molded part but at a much lower tooling cost than injection molding or other alternative processes such as RIM molding and structural foam molding. Pressure formed plastic parts are also a good alternative to sheet metal, fiber glass or wood. Pressure forming is especially advantageous when using a female mold. The mold can even be textured just like an injection mold so the texture is formed directly into the finished part.
Features such as style lines, molded-in textures, tight corners, ribbing, and embossed wording & logos may also be incorporated into the formed part. In summary, advantages include:
- High level of detail and ability to confirm to stringent tolerances
- Lower cost tooling than injection molding (less than 1/3 injection molding cost)
- Ability to form parts with fine cosmetic or functional details, such as vents or louvers, undercuts, lettering and logos
- Highly cost effective for low to moderate quantities (300 – 5,000)
- Ability to form very large parts
- Rapid prototyping and quick time to market
Applications:
Typical applications of pressure forming would be bezels, bases, housings, aesthetically designed enclosures, covers, and equipment panels. Pressure formed parts are very commonly used for medical devices, recreational equipment, outdoor housings, transportation and construction equipment, retail items & point-of-purchase displays, and outdoor equipment.
Plastic pressure forming is an excellent alternative to injection molding or structural foam molding in many applications, especially in runs of moderate volumes. Pressure formed parts are available in a large variety of colors, materials and different textures utilizing common thermoplastic materials.
Some of the materials most commonly utilized in plastic pressure forming are as follows:
- ABS – impact resistant, available in a variety of colors, textures, flame retardant grades
- PC – impact & high temperature resistant
- HDPE – inexpensive; impact, chemical and cold temperature resistant
- TPO – good durability, impact resistant
- HIPS – cost effective, available in a variety of colors
- PVC – impact resistant, available in a variety of colors, textures, flame retardant grades
Universal Plastics will share our expertise in thermoplastics to help you to find the right material for your part.
Pressure Forming Capabilities at Universal Plastics:
Universal Plastics’ capabilities include a long legacy of expertise in pressure forming across various industries including medical devices, electronics, enclosures, etc. Universal Plastics is the largest precision heavy gauge custom thermoformer in the Northeastern US with an asset base of 22 pressure formers, 14 vacuum formers and 26 5-axis trimming machines, supplying our customers with vacuum forming, pressure forming, including twin sheet forming and complex assemblies, with part sizes up to 12’ x 9’. In addition, we offer in-house tooling, an experienced engineering staff, and a full complement of secondary/finishing services, including our new state of the art paint booths which can produce automotive quality finishes. With a range of rotary formers, rapid manufacturing processes, and a global supply chain, we can produce thermoformed parts at the most competitive prices. Universal Plastics’ extensive experience designing pressure formed parts gives us the confidence to say we are experts in understanding the process advantages and limitations. Like all thermoforming, pressure forming is a process that is half science and half art – and we know we can make your part right the first time. In addition to custom thermoforming, Universal Plastics also offers injection molding (including gas assist and structural foam molding) and custom blow molding. We would be glad to talk with you about the optimal process for your needs.
For more information about pressure forming and how Universal Plastics can put our expertise to work for you, please contact us.